Spodumene ore is one of the principal sources of lithium. It occurs in muscovite type and lepidolite type granitic pegmatite. It is a mineral of metasomatic origin in the process of pegmatite, which is often associated with lepidolite, beryl, niobium tantalite, tourmaline, muscovite, etc., and belongs to silicate minerals with these gangue minerals. During spodumene processing, it generally adopts the flotation method for lithium ore.
In recent years, with the rapid increase in demand for positive electrode materials for new energy vehicles, the price of spodumene concentrate is kept increasing, and many lithium ore beneficiation plants have begun to expand the production of lithium ore. The client needs to choose the appropriate and correct spodumene separation process for the rational development and utilization of lithium ore resources. The spodumene ore beneficiation process includes crushing and screening, grinding and classification, flotation purification, tailings magnetic separation, etc.
Spodumene Experimental Steps
- Sample spodumene ore crushing screening
During crushing and screening operations, there will need two crushers for crushing.
Put rock spodumene into the jaw crusher for coarse crushing, then put the crushed products into the secondary crusher for fine crushing, and after the crushing process, put the fine spodumene ore into the manual screen for screening. Spodumene on the screen will send to the secondary crusher for fine crushing. The screened spodumene ore enters the next processing machine. This processing flow ensures the processing efficiency of raw ore and the recovery rate of concentrate.
- Spodumene grinding classification
After crushing and screening, the material enters the grinding and classification process. Put The materials into the ball mill for grinding, and the products after grinding enter the hydrocyclone or spiral classifier for classification. Because spodumene contains other argillaceous substances, the graded slurry will be transferred to an inclined plate thickener for desliming and concentration operations. After a period of sedimentation, the concentrated spodumene slurry will discharge from the bottom of the thickener and enters the following selection process.
- Spodumene flotation
Spodumene processing generally adopts The flotation method. The specific process flow is the concentrated spodumene slurry will enter the flotation machine for a rough selection. After selection, the spodumene coarse concentrate will proceed to the next step of the selection operation, and the tailings will undergo a sweep process. The three-stage selection will improve the recovery rate of spodumene concentrate and avoid material waste. The spodumene concentrate product can settle in the concentrate warehouse for storage and further processing.
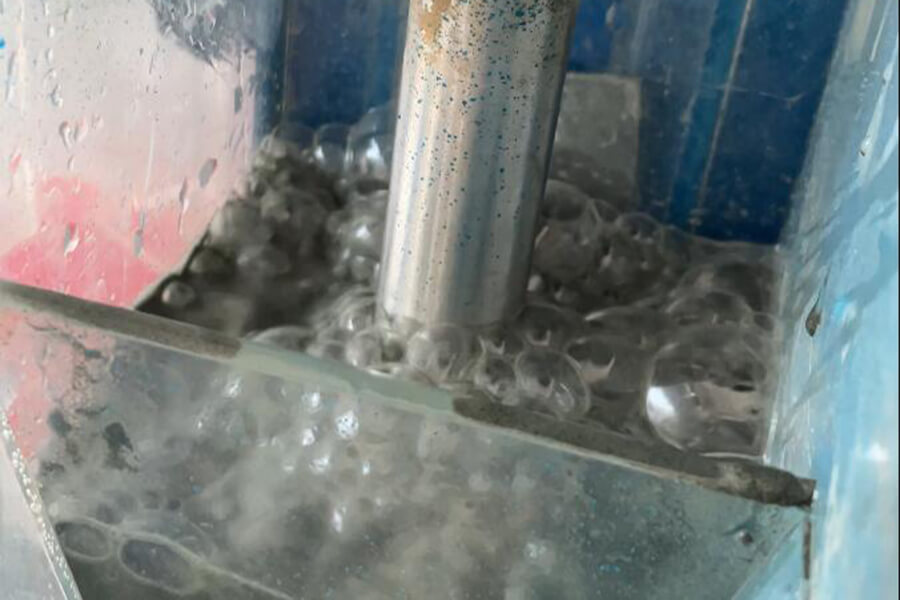
- Magnetic separation of spodumene tailings
The purpose of treating spodumene tailings is to improve the recovery rate of spodumene concentrate. After the rough selection, the tailings of spodumene will enter the sweep process for treatment. Due to the presence of mica and other impurities in spodumene tailings, if they enter the high-intensity magnetic separator directly for separation, it may cause blockage in the medium box and affect the effectiveness of high-intensity magnetic iron removal. So to ensure and improve the iron removal effect, we can add a high-frequency vibrating screen before the spodumene tailings enter the weak magnetic separator. It will remove impurities in the tailings and ensure the operation of the iron removal process. To obtain high-quality feldspar powder, the tailings after iron removal will go to one weak magnetic separator and two high-intensity magnetic separators.
The above is an introduction to the process flow of spodumene beneficiation, which is for reference. According to the features of the spodumene, we will provide a specific design for you. Don’t replicate the process flow of other mineral processing plants. It is necessary to conduct a test before ore selection.
Spodumene Beneficiation Test
- Lab Jaw crusher for primary crushing. Put 100mm rock spodumene ore into the lab jaw crusher, and the lab jaw crusher’s fixed and movable jaw will crush the material to 10-40mm. The crushed material will discharge from the discharge port at the bottom of the jaw crusher.
- Lab Hammer crusher for second crushing. Pour the 10-40mm spodumene ore into the hammer crusher, and the hammer head inside the hammer crusher will rotate and crush the material to fine particle sizes, such as 0-10mm and 0-5mm. The discharge size is adjustable.
- Ball mill for grinding minerals. Its principal function is to grind small particle materials into powder form. Pour the material particle size of 25mm into a ball mill to grind the material into powder of 0-1mm or 0-200mesh by grinding steel balls inside.
- Manually screen the powder material. Pour the material ground by the ball mill into a manual screen, screen out 0-200 mesh of material for flotation, and pour over 200 mesh material into the ball mill for further grinding if it exceeds 200 mesh.
- Flotation machine for enriching lithium concentrate. The laboratory flotation machine is sorting equipment that requires the addition of conventional reagents. Different materials also require different chemicals for separation. Pour the slurry into the tank and dilute it with water to the required concentration; Start the motor and add an appropriate amount of flotation agent according to the experimental requirements; When the foam generates in the tank, turn on the switch of the scraper part to start flotation; when arriving the specified flotation time, turn off the motor to stop the impeller and scraper from running.
- Analyze the spodumene ore concentrate or tailings to confirm their chemical composition and impurity levels. These data will help evaluate the effectiveness of the beneficiation process and guide necessary modifications. Optimize the beneficiation process parameters based on flotation and magnetic separation experiment results. It may involve adjusting the grinding particle size, reagent dosage, or process conditions to achieve the required concentrate grade and recovery rate.
- Reports. Compile the results of Spodumene ore beneficiation experiments and prepare a comprehensive report summarizing the results. The information should include testing procedures, observation results, and recommendations for further steps in the beneficiation process.
Mineral processing experiment is for selecting ore and getting processing flow. The results of beneficiation experiments not only have a direct effect on the reasonable determination of the process flow, equipment selection, product plan, and technical and economic indicators of beneficiation design but also serve as the basis for whether the beneficiation plant can smoothly achieve the design index and obtain economic benefits after production. The properties of ores in different regions are ever-changing, and their beneficiation processes and conditions vary. Asia Africa International provides laboratory mineral experimental service, and offers accurate and reliable test results to meet the different needs of customers. Our advanced equipment, experienced engineers, and technical personnel help our clients better optimize their mining operations. Welcome to inquire and consult!