Selective separation of tantalum and niobium from brine slag by understanding the complex properties of these metals, we aim to design customized extraction methods that increase efficiency and reduce environmental impact. These laboratory tests provide valuable insights into the potential for sustainable resource recovery from industrial waste streams, paving the way for a more circular economy approach in metal production.
Our laboratory equipment enables precise control of parameters such as temperature, pressure, and chemical reactions to increase the purity of extracted minerals. We will use a recycling machine with carpet to enrich the concentrate and then use a suspended cone or shaker to extract the tantalum-niobium concentrate. Choose a shaking table or a suspended cone concentrator to process fine-grained minerals. After laboratory testing, we can choose the equipment with the best mineral processing effect.
About Separating Tantalum- Niobium Form Brine Slag
Tantalum and niobium are two valuable metals commonly found in brine slag (a by-product of salt production). The properties of tantalum and niobium in brine residues play an essential role in their extraction potential. Tantalum is known for its high melting point and corrosion resistance, making it an ideal material for electronics and surgical instruments. Meanwhile, niobium‘s superconducting properties make it vital for applications such as MRI machines and particle accelerators. A key aspect to consider is the complex chemical composition of brine slag, which can vary depending on the source and processing method.
In addition, other impurities in the brine slag can affect the quality and purity of the extracted metals, requiring complex separation techniques. Understanding how these properties interact in brine slag is important for optimizing recycling while minimizing environmental impacts. Waste generation is minimized by effectively separating these tantalum-niobium ores, and responsible mining practices are promoted.
laboratory equipment
Vibration Recycling Machine with Carpet
Separating tantalum and niobium from brine residue using a vibration recovery machine equipped with a unique carpet is a breakthrough innovation in mineral processing. The method ensures efficient separation of valuable metals from scrap and utilizes vibration technology to minimize environmental impact. The machine’s ability to effectively separate tantalum and niobium particles from complex brine slag matrices highlights its potential for large-scale commercial applications.
By adopting this advanced recycling technology, industries can significantly reduce their reliance on traditional mining methods, reducing energy consumption and overall production costs. Using a vibrating recycling machine with custom-made carpets highlights a paradigm shift towards sustainable resource management in the tantalum and niobium extraction process. This innovative approach improves operational efficiency and highlights the importance of the mining industry adopting environmentally friendly beneficiation practices.
Main function:
Its main function is initially to enrich materials into fine-grained materials. Materials are selected and enriched through water flow and the gravity of the material itself. Then, gravity separation is performed to obtain tantalum-niobium concentrate.

shaking table
Subjecting the slag to high-frequency vibrations on a vibrating table separates valuable minerals from the waste based on their different densities. This innovative technology improves the overall recovery rate of tantalum and niobium and reduces the environmental impact by minimizing the amount of waste generated during the extraction process.
Additionally, utilizing shakers for tantalum and niobium extraction provides a more cost-effective solution than traditional methods, requiring less energy and resources while delivering higher final product purity. Customizing shaker settings allows for precise separation process control, ensuring optimal performance and maximizing throughput.
Main functions: The shaking table separates fine-grained materials and is the most commonly used gravity separation in mineral processing operations. It is mainly used to recover fine-grained minerals of 0-2mm. Mechanical shaking and water flow separate the mineral particles according to density. Multiple products can be obtained simultaneously, and the mineral zoning on the bed surface is obvious. We can get concentrate, middlings, and tailings.
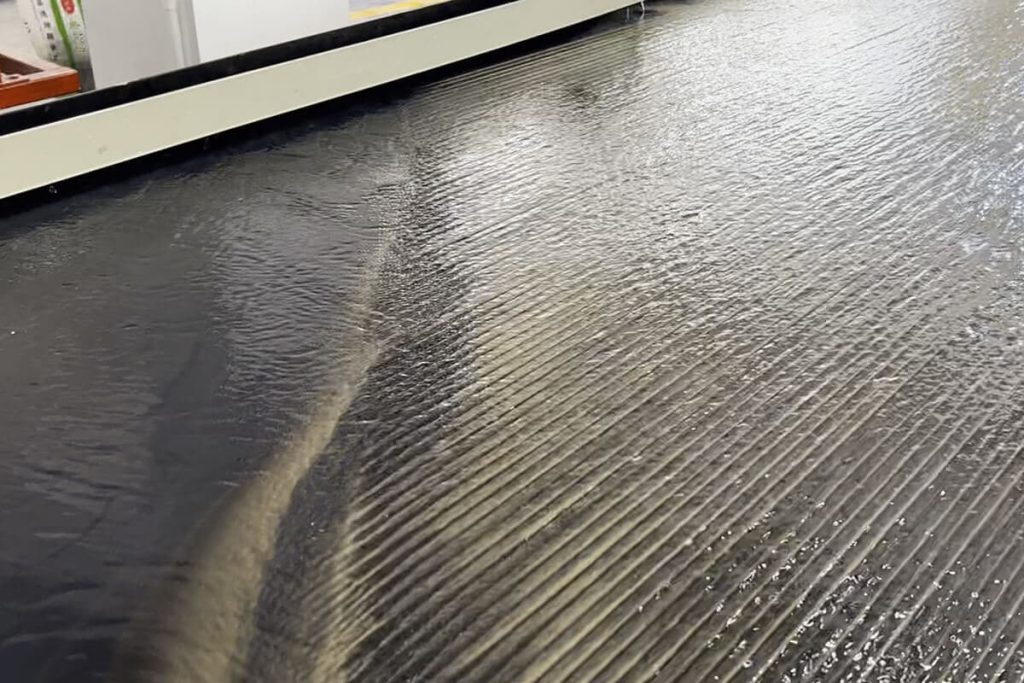
Suspended vibration cone concentrator
A key advantage of the suspended vibrating cone concentrator is its ability to handle a variety of feed sizes, making it a versatile and adaptable solution for processing different types of ore. By harnessing the power of vibration, this advanced concentrator can achieve high concentration ratios and recover valuable metals with minimal energy consumption. As industries continue to seek sustainable practices and greener solutions, separating tantalum and niobium through suspended vibrating concentrators provides a highly effective strategy for improving resource efficiency and reducing carbon footprints.
Main function:
It is a high-efficiency, fine-grained gravity mineral processing equipment. When the material is fed into the ore feeder, the slurry forms a fan shape and flows to the periphery. Through its gravity and gyrating vibration force, the material brings minerals of different densities into the tailings tank, the middle ore tank, and the concentrate tank in sequence.
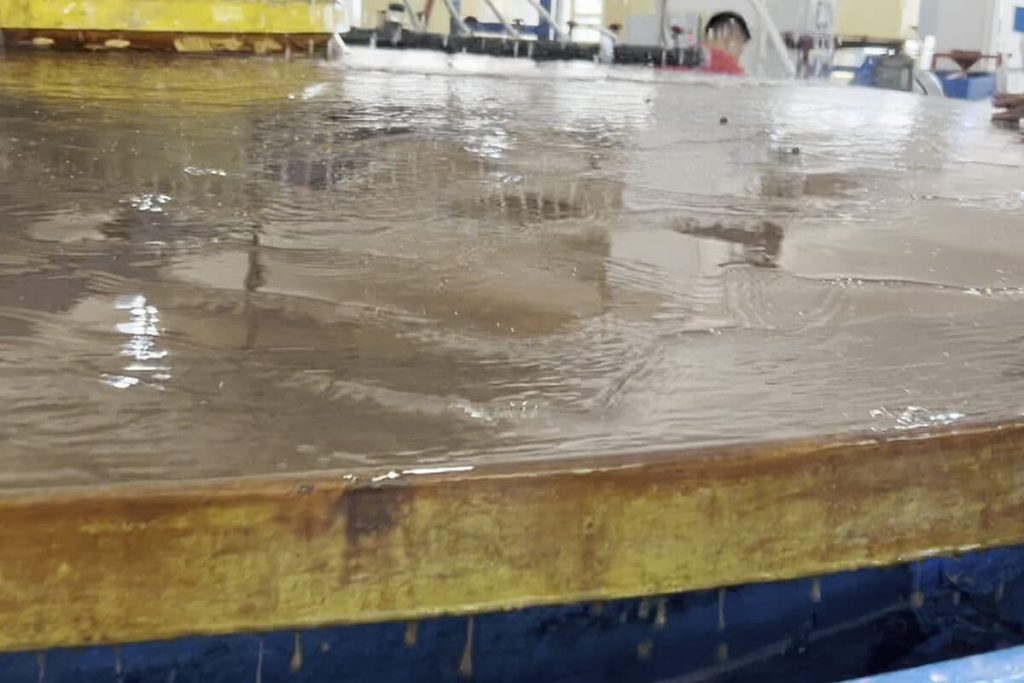
Using advanced technology and equipment in a laboratory environment enables researchers to optimize process parameters to increase efficiency and productivity. The extraction of tantalum and niobium from brine residues using laboratory vibrating blanket machines, shaking tables, or suspended cone concentrator equipment is a promising method for recovering these valuable metals. Asia-Africa International can provide various mineral processing testing services and high-quality equipment. The purpose is to conduct preliminary research on possible test plans, process flows, and selection conditions and provide an important basis for subsequent large-scale production.