Magnetic separation refers to a mineral processing method that uses magnetic equipment to separate magnetic materials from other materials based on the magnetic properties of the materials. The machines used for this operation are magnetic separation equipment. Laboratory magnetic separation equipment uses magnetic fields to effectively separate target substances from complex mixtures, allowing researchers to precisely separate specific molecules or particles. It is widely used in the separation of tantalum niobium ore and iron ore; the purification of quartz, kaolin, bentonite, wollastonite, feldspar, talc and other non-metallic minerals. The performance and process parameters of magnetic separation equipment are important factors affecting the iron removal effect. Usually, we can first analyze the five common laboratory magnetic separation equipment through laboratory testing.
1. Wet drum magnetic separator
The wet drum magnetic separator is suitable for wet magnetic separation of magnetite, pyrrhotite, roasted ore, ilmenite and other materials with a particle size of less than 3mm. It is also used for iron removal of coal, non-metallic ores, building materials and other materials. The device is unique in its ability to process a large number of materials while maintaining a consistent magnetic field strength. Additionally, its compact size makes it ideal for small laboratory environments, allowing researchers to conduct experiments easily and efficiently.
Working Principle
When the slurry of the wet magnetic separator flows into the magnetic field area, the highly magnetic minerals in it are adsorbed on the surface of the cylinder, so that the weakly magnetic and non-magnetic minerals are sorted and eliminated. When the material is adsorbed on the surface of the cylinder, the highly magnetic minerals in the material are taken out of the magnetic field area as the cylinder rotates. Due to the high-speed rotation, the number of magnetic tumbles of the magnetic particles inside is much higher than that of ordinary magnetic separators. After sorting, the weakly magnetic minerals are separated into magnetic substances and non-magnetic substances, which are discharged from their respective discharge ports.
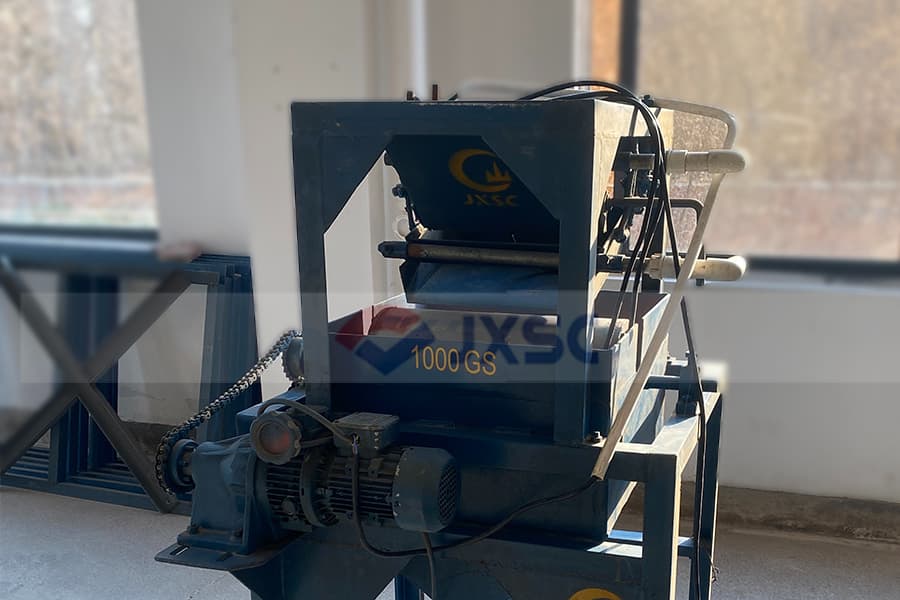
2. High intensity dry magnetic separator
This magnetic separation equipment generates high magnetic field forces to separate complex mixtures accurately and efficiently. This high-gradient non-uniform magnetic field can be used to separate extremely weakly magnetic micro-particle materials that are difficult to be sorted by ordinary magnetic separators, and greatly reduce the lower limit of sorting particle size (can be reduced to 1 μm), improving sorting indicators. Whether it is dry magnetic separation of magnetite, pyrrhotite, roasted ore, ilmenite and other materials, this equipment provides reliable performance in separating valuable materials from waste. The magnetic system of the high-gradient strong magnetic separator is made of high-quality ferrite materials or compounded with rare earth magnets. It has multiple drums and is an ideal equipment choice for fast and efficient separation.
Working Principle
The materials are evenly fed to the upper magnetic field area of the rotating drum through the electromagnetic vibrating feeder. The magnetic material is adsorbed on the surface of the drum and rotates with the drum. The rotating cylinder throws the non-magnetic materials away from the cylinder, and the magnetic materials are attracted to the cylinder by the strong magnetic field force. The magnetic and non-magnetic materials can be easily separated by the separation plate.
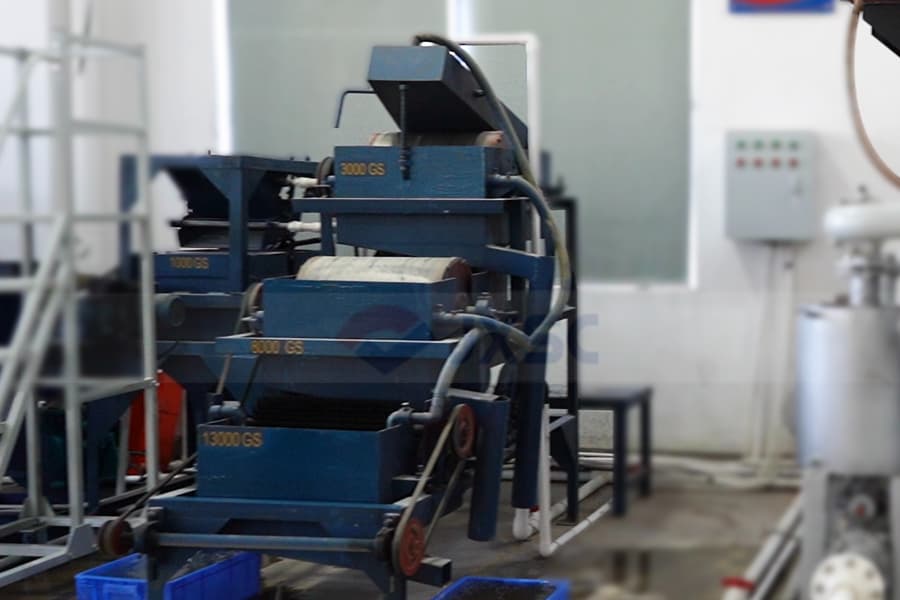
3. Three-disk magnetic separator
Dry separation of titanium ore, tungsten tin ore, chromite, niobium tantalum ore, limonite, zircon, gold red, solitary, andalusite, blue quartz, feldspar, quartz and other metal minerals with different magnetic properties ‘s selection. It is primarily capable of handling samples of various sizes, making it suitable for a variety of lab research applications. It can achieve one-time separation of three or more minerals, and its high accuracy and reliability make it the first choice for analyzing mineral samples with complex compositions. Adjustable parameters on the equipment allow customization to specific requirements, providing flexibility and versatility for processing various types of materials. This improves product quality and purity, ensuring better overall results in laboratory research and industrial applications.
Working Principle
As the feed materials enter the top of the rotating drum, they are subjected to a strong magnetic field generated by a high-intensity disk. These discs attract paramagnetic and weakly magnetic particles and separate them from non-magnetic materials, resulting in clean separation. Its adjustable disc gap setting allows for precise control of magnetic field strength and the ability to effectively separate different mineral types.
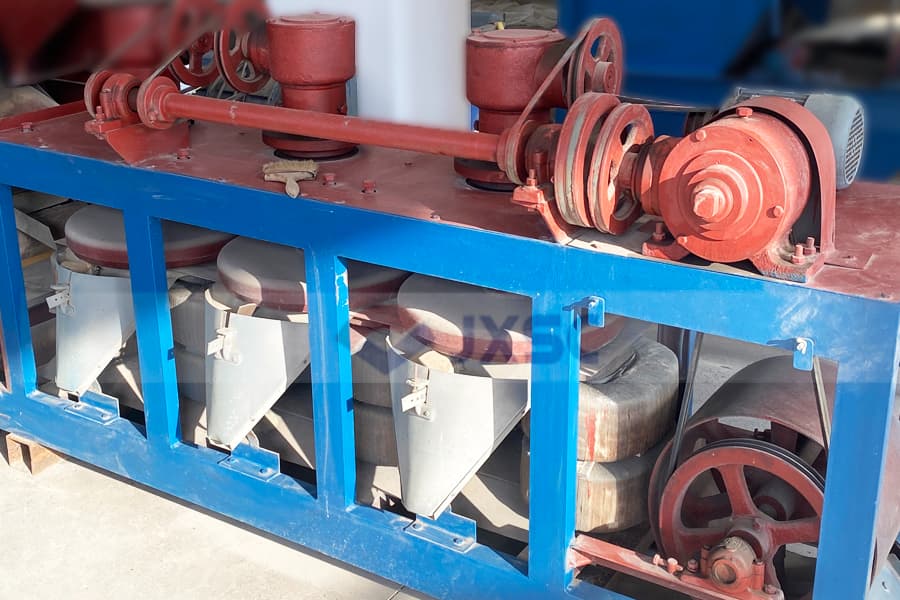
4. Plate magnetic separator
The plate magnetic separator has a compact design and can be easily integrated into existing laboratory setups. Especially for iron removal and purification of quartz sand, feldspar, nepheline ore and kaolin. Its ability to rapidly separate target materials makes it an indispensable tool for researchers working with biological samples, nanoparticles, and other complex mixtures. By utilizing powerful magnets arranged on a flat surface, this separator quickly and efficiently removes iron-containing contaminants from liquid or dry samples. This magnetic separator provides a non-invasive method to separate magnetic materials without causing any damage or alteration to sample integrity.
Working Principle
The slurry enters the uniform feeding device of the magnetic separator through the feed inlet. After being fully dispersed, it is evenly sprinkled on the unloading belt on the upper part of the magnetic plate. Under the action of gravity, the slurry flows downward along the inclined direction of the magnetic plate. The ferromagnetic substances contained in the slurry are firmly adsorbed on the iron unloading belt under the strong magnetic field. The motor rotation device drives the iron unloading belt to move upward along the inclined direction of the magnetic plate. At the same time, the adsorbed ferromagnetic substances are brought into the iron unloading area, where they are flushed by water into the tailings hopper and collected centrally. The non-magnetic slurry continues to flow downward along the magnetic plate, flows into the concentrate hopper and is collected centrally.
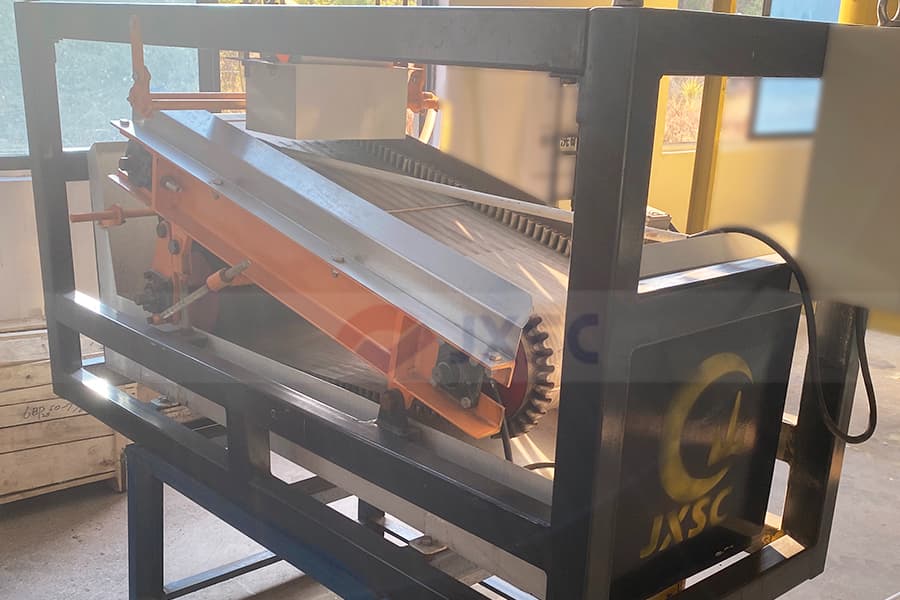
5. Slurry magnetic separator
Slurry magnetic separator is a common equipment in lab magnetic separation test and is often used to purify and remove impurities from quartz, feldspar, kaolin and other non-metallic minerals. It is mainly used to clean contaminated raw materials that need to reduce iron impurities. It effectively captures target particles while ensuring minimal interference from non-magnetic components. Fully automatic without manual operation, the iron removal operation is convenient. By adjusting parameters such as magnetic field strength, flow rate and particle size distribution, optimal separation efficiency and purity can be achieved in the sample. Not only can research capabilities be enhanced, but experimental workflows can also be streamlined, increasing productivity and accuracy.
Working Principle
As the slurry enters the separator, powerful magnets create a magnetic field that attracts and retains the magnetized particles, separating them from the rest of the slurry. When all the slurry passes through the mineral magnetic separator, close the slurry inlet valve and the slurry outlet valve, and discharge the remaining slurry in the magnetic separator through the return slurry valve. Then cut off the magnetism, close the slurry inlet valve, slurry outlet valve and return slurry valve, open the iron discharge valve, and discharge the iron-containing substances adsorbed in the magnetic medium.
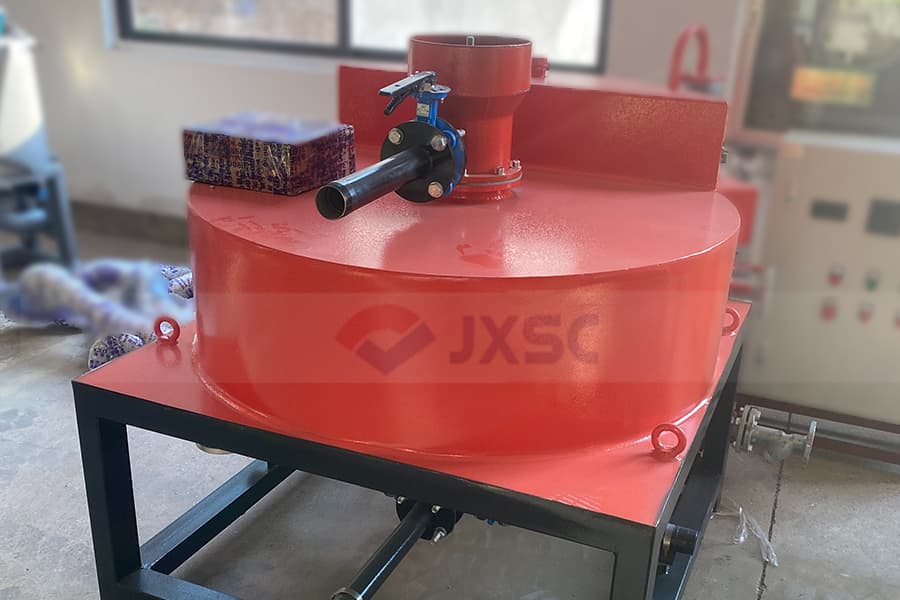
In laboratories, common magnetic separation equipment mainly includes the above five types: wet drum magnetic separator, high-intensity dry separation, three-disk magnetic separator, slurry and plate magnetic separator. By understanding the different types of magnetic separation equipment, researchers can choose the option that best suits their specific needs. Each magnetic separator has unique advantages, and with proper maintenance and compliance with operating guidelines, these devices can increase productivity and accuracy in the laboratory environment. We (Asia-Africa International) will develop the best laboratory magnetic separation equipment based on your mineral information. You can also conduct testing services on minerals first to achieve maximum recovery rate while selecting the most suitable equipment.