Antimony and its compounds are important raw materials for industrial production and people’s lives. They are widely used from flame retardants to lead-acid batteries. With the continuous exploitation of antimony metal mines, antimony resources are constantly decreasing, and the ore grade is getting lower and lower. Separating antimony from ore is very complicated and requires precise methods to improve the recovery rate while minimizing the environmental impact. Antimony ore beneficiation mainly adopts flotation process, and gravity separation is an auxiliary process. Then, different flotation equipment and methods will affect the effect of recovering concentrate. Different reagents and conditions need to be used through mineral processing experiments to optimize the selectivity and efficiency of the extraction process.
The laboratory antimony ore flotation test process mainly adjusts the flotation process by adjusting variables such as flotation equipment, pH value, and reagent amount to maximize the output while minimizing unnecessary pollutants. Provide a reliable basis and mineral processing solution for the smooth commissioning of the general election project.
Antimony ore phase analysis
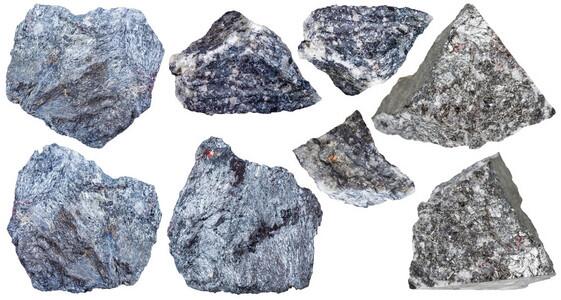
Chemical composition analysis: Determine the content of antimony, sulfur, and other elements in antimony ore through chemical analysis methods.
Ore structure analysis: Observe and analyze the crystal structure, crystal morphology, fracture morphology, and other characteristics of the ore through microscopes, electron microscopes, and other instruments to understand the composition, mineral composition, and structural properties of the ore. Antimony mineral types, such as stibnite, antimony chalcanthite, etc., and their embedding characteristics.
Particle size analysis: Measure the particle size distribution of antimony ore through instruments such as laser particle size analyzers to understand the particle size and distribution of ore, which has an important guiding role in the ore grinding, beneficiation, and other processes of the ore.
Spectral analysis: Use instruments such as spectrometers to conduct elemental analysis, ore type identification and ore composition changes on antimony ore.
antimony ore flotation test process
The process of antimony ore flotation experiment usually includes the following steps, each of which needs to be adjusted and optimized according to the properties of the ore. The specific process is as follows:
1. Ore sample preparation, crushing and grinding
Collect representative ore samples from the mine to ensure that the samples are uniform and representative. Crush the samples to a particle size suitable for flotation (usually -200 mesh accounts for 70%-90%) by using a laboratory crusher and ball mill. Determine the chemical composition (such as antimony, arsenic, and sulfur content) and mineral composition of the ore sample to determine the dissociation characteristics of the target mineral and the gangue mineral.
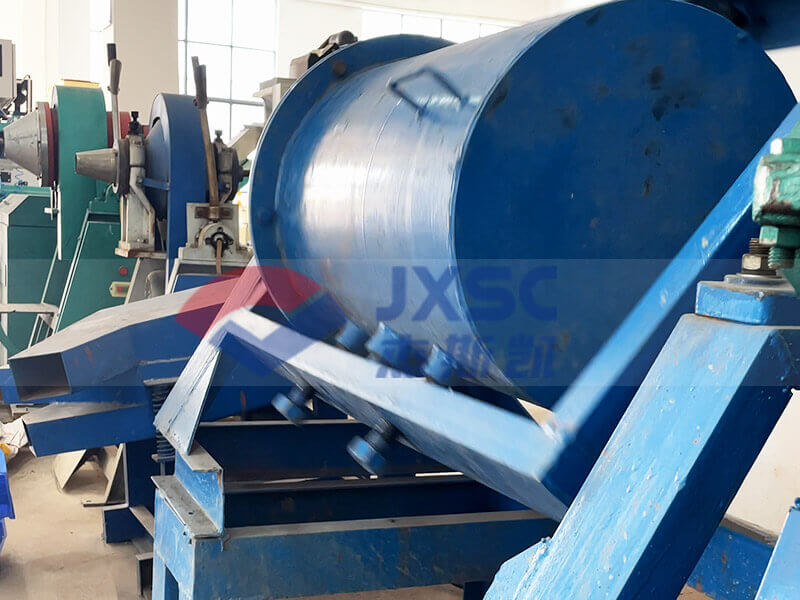
2. Determine the flotation reagent
Collectors such as butyl xanthate, isobutyl xanthate, and ethyl thiocyanate are commonly used in antimony ore flotation;
- Frothers: pine oil, ethyl xanthate, etc.
- Adjusting agents: lime, sulfuric acid, sulfuric acid, etc. adjust the pH of the ore pulp.
- Activators or depressants: copper sulfate, sodium sulfide.
The specific selection will determine the flotation reagent based on the properties of the mineral, while laboratory tests use small reagent dosages to test whether it is feasible.
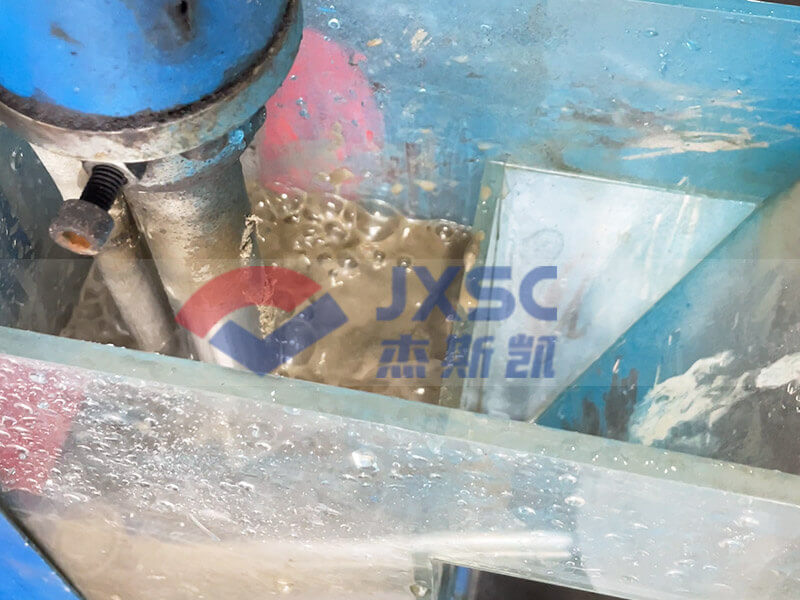
3. Antimony ore Flotation process
Design the flotation process, which may include: one roughing separation: extract the main antimony minerals; multiple concentration: improve the grade of antimony concentrate; scavenging separation: treat the roughing tailings and recover the residual antimony minerals.
Pour the slurry into the flotation machine and adjust the slurry concentration (usually 20%-30%). Add water and adjuster: Add an appropriate amount of water to adjust the slurry concentration to 20%-30%, and then add an adjuster to adjust the slurry pH (antimony ore usually uses pH 5-7). Add an activator, collector, and frother. Stir evenly after each addition to ensure the reagent is in full contact with the slurry. Start the flotation machine and observe the mineral foam layer.
(In this process, the order of adding reagents and the stirring time must also be strictly controlled to ensure the effect of the reagents.)
4. Optimization of flotation parameters
Based on the preliminary flotation experiment, these parameters can be adjusted to optimize the beneficiation effect, such as slurry pH value, reagent type, dosage, flotation time, stirring speed, etc.
5. Experimental analysis and summary
Record experimental parameters, including reagent dosage, flotation time, gas flow, pulp pH, etc. Compare concentrate grade, recovery rate, tailings loss, and other data. Adjust the reagent ratio and flotation parameters to optimize the process according to the experimental results. Evaluate the cost and effect of reagent dosage and determine the optimal recovery rate of antimony concentrate. Summarize the optimal flotation process and equipment selection based on the experimental results to form a final experimental report.
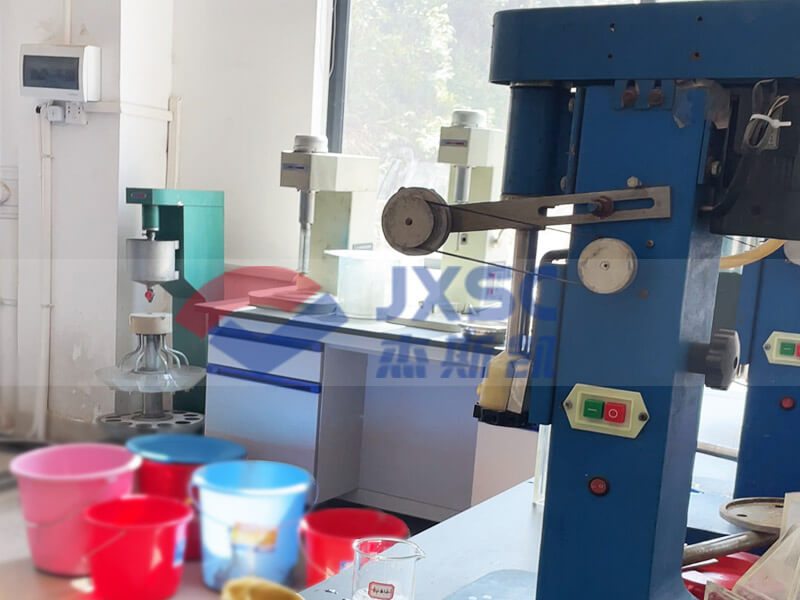
Laboratory-scale flotation studies provide a deeper understanding of the fundamental processes that control particle interactions during flotation. By analyzing factors such as particle size distribution, hydrophobicity, flotation reagents, pH, and more, researchers have gained valuable insights to help larger beneficiation plants successfully be commissioned and maximize concentrate recovery. Antimony ore flotation experiments help determine the equipment best suited for a specific ore type and provide insights into how design improvements can achieve more efficient operations. Asia-Africa International(JXSC) supports customized various types of mineral processing experimental services and equipment. Contact us for more details!