Laboratory Flotation Testing
Our laboratory mineral flotation tests are performed on small-scale samples in a laboratory setting. It can separate and enrich non-ferrous, ferrous, and non-metallic minerals. It involves adding reagents to facilitate the binding of specific minerals to air bubbles, which then float to the surface for further recovery. To determine the reasonable values of various index parameters in the flotation process, mineral processing experiments will be carried out to ensure the best recovery rate and product quality in mining operations.
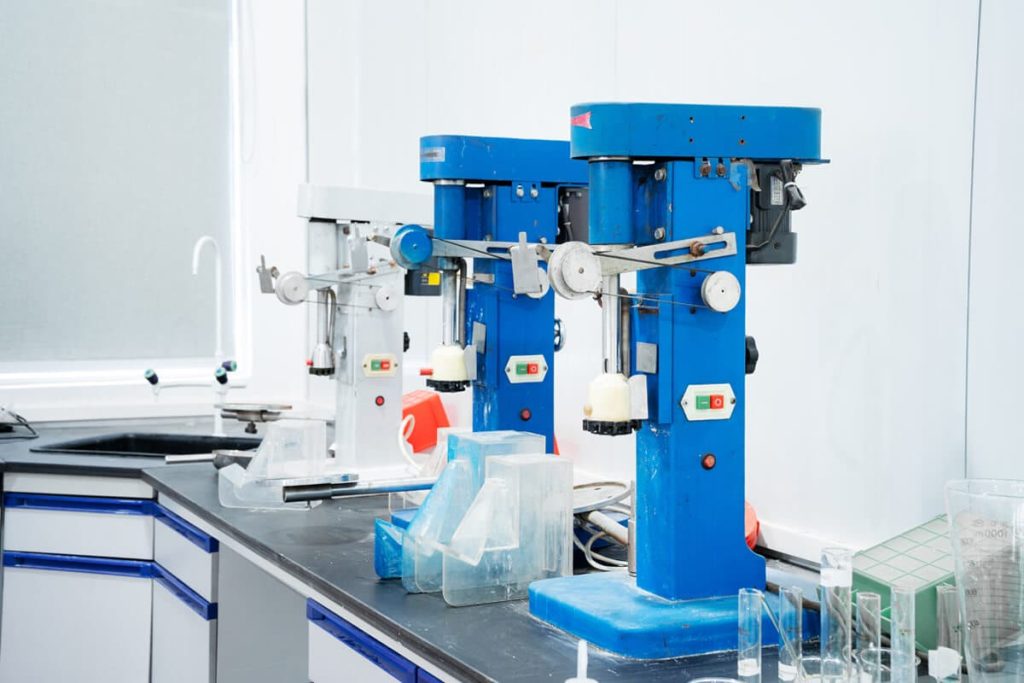
Lab Mineral Flotation Testing
Introduction
Lab mineral flotation testing is used in mineral processing to evaluate the feasibility and efficiency of separating valuable minerals from their associated gangue. This testing process provides crucial information for designing and optimizing flotation circuits in industrial-scale mineral processing plants. Engineers and researchers can determine the optimal operating parameters and reagent dosages required for successful mineral separation by simulating flotation conditions in a laboratory setting.
Work Principle
Laboratory mineral flotation tests are based on the ability of certain minerals to selectively attach to air bubbles introduced into a finely ground ore suspension. By adjusting operating conditions and adding specific chemical reagents, valuable minerals can be attached to the air bubbles and rise to the surface to form a foam layer. The foam containing the desired minerals is then collected while the gangue minerals sink. This separation process is called froth flotation.
Main Testing Steps
Step 1: Sample Preparation
The mineral ore sample is collected and prepared by crushing, grinding, and sizing to ensure a representative particle size distribution.
Step 2: Pulp Preparation
The sample is mixed with water to form a slurry called pulp. The desired solid concentration or pulp density is determined based on the specific testing objectives.
Step 3: Conditioning
Various reagents, such as collectors, frothers, and modifiers, are added to the pulp to modify the mineral surfaces and create suitable conditions for flotation.
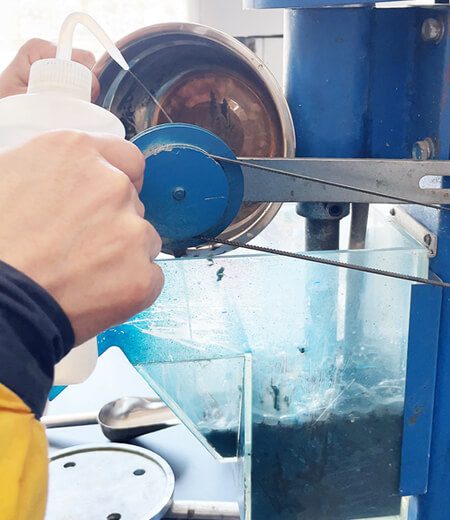

Step 4: Flotation
The conditioned pulp is introduced into a flotation cell or equipment, where air or gas is bubbled through the mixture. The air bubbles selectively attach to the target minerals, carrying them to the surface as a froth layer.
Step 5: Froth Collection
The froth containing the valuable minerals is skimmed off the top of the flotation cell, typically using paddles or automated devices.
Step 6: Analysis
The collected froth is analyzed to determine the mineral content and grade, providing valuable data for process optimization and subsequent flotation stages.
Equipment For Flotation Experiment
Commonly used equipment in lab mineral flotation testing
- Flotation Cells
- Agitators
- pH and Temperature Control Equipment
- Analytical Instruments
- Reagent Preparation Equipment
- Froth Collection Devices
- Filtration or Dewatering Equipment
Note: The specific equipment used may vary depending on the laboratory setup and the nature of the mineral being tested.