Optical Separation
Asia-Africa International offers mineral optical sorting services that play a crucial role in the mining industry by providing advanced technologies, expertise, and analysis to optimize ore processing operations. It has state-of-the-art optical sorting equipment, knowledgeable staff, and a research-oriented environment. Asia-Africa International focuses on developing innovative solutions and conducting in-depth studies to improve mineral processing efficiency, productivity, and profitability through optical separation techniques.
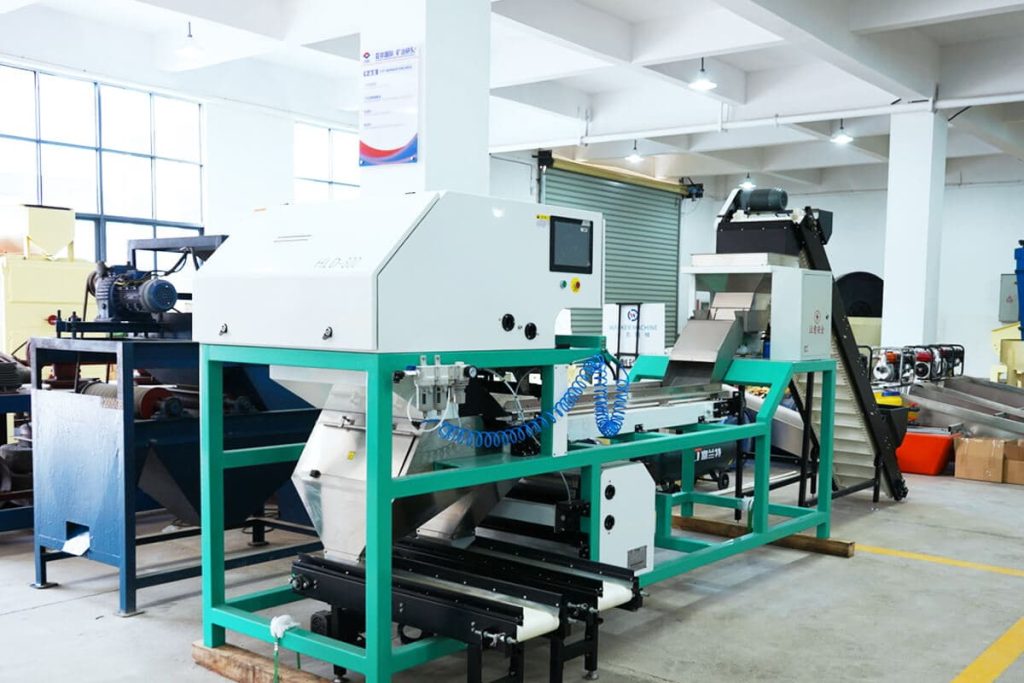
Lab Optical SeparationTesting
Introduction
Optical separation refers to separating or sorting objects or particles based on their optical properties. It utilizes various optical techniques and devices to distinguish and separate objects based on their interaction with light. Optical separation is used in recycling, mining, and food processing industries.
In mining, optical separation refers to using optical techniques and equipment to separate valuable minerals or ores from gangue (unwanted material) based on their optical properties. This technique is also known as optical sorting or ore sorting. Optical sensors, cameras, and other devices capture the optical data, which is then processed and analyzed using sophisticated algorithms and software. Based on the optical properties of the particles, the system can identify and separate valuable minerals from the gangue.
Optical Separation Features
- Increased Efficiency
- Higher Recovery Rates
- Reduced Environmental Impact
- Real-time Monitoring
- Sorting Complex Ores
- Safety and Automation
Work Principle
The working principle of the optical separator is to use ultraviolet rays, visible light, infrared rays, etc., to contact objects to produce absorption, reflection, and transmission phenomena, to detect materials, and then use compressed air, water, or mechanical arms to separate target minerals and non-target minerals. The process is as follows:
- The product is fed into the hopper, which provides the product with a vibrating plate that carries the product onto the feed chutes.
- The product free flows down the chutes and is viewed by the sensors from both sides. The sensor outputs go to the signal processor, and if the processor detects a “reject image,” it fires the relevant ejector.
- The ejector diverts the impurity from the product stream with a focused jet of compressed air.
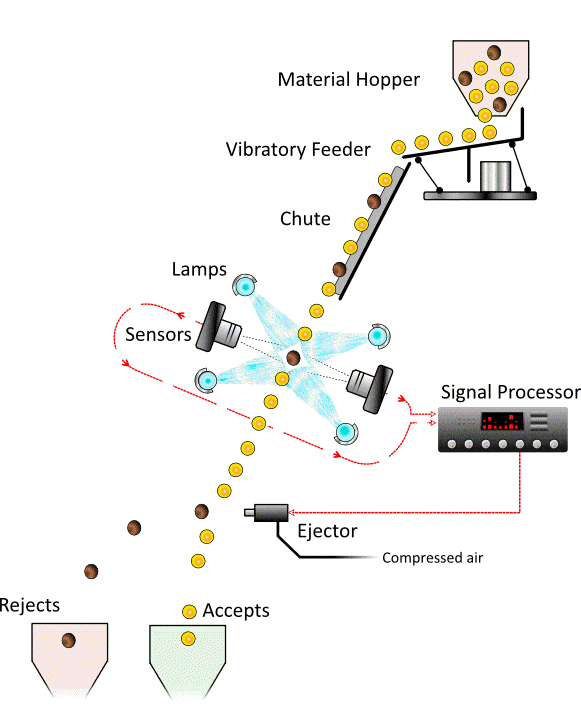
Main Testing Steps
Step 1: Initial Assessment
Assess optical separation’s feasibility and potential benefits for the specific mining operation.
Step 2: Sample Collection & Preparation
Supplying sufficient sample quantity is necessary to conduct comprehensive testing and obtain statistically significant results. And the collected ore samples are prepared for testing. It typically involves crushing, grinding, and reducing the particle size to a suitable range for optical sorting analysis.
Step 3: Optical Sorting Equipment Setup
We set up the optical sorting equipment in the laboratory. It includes calibrating the sorting machine, configuring the sensor settings, and ensuring the system’s proper functioning. The equipment setup is tailored to the specific characteristics of the ore samples being tested.
Step 4: Optical Separation Testing
The prepared ore samples are fed into the optical sorting equipment, and the sorting process is initiated. The system captures individual particles’ optical data, such as color, reflectance, or other optical properties, as they pass through the sorting zone. The sorting performance and efficiency are assessed by monitoring the separation outcomes and evaluating the sorting accuracy.
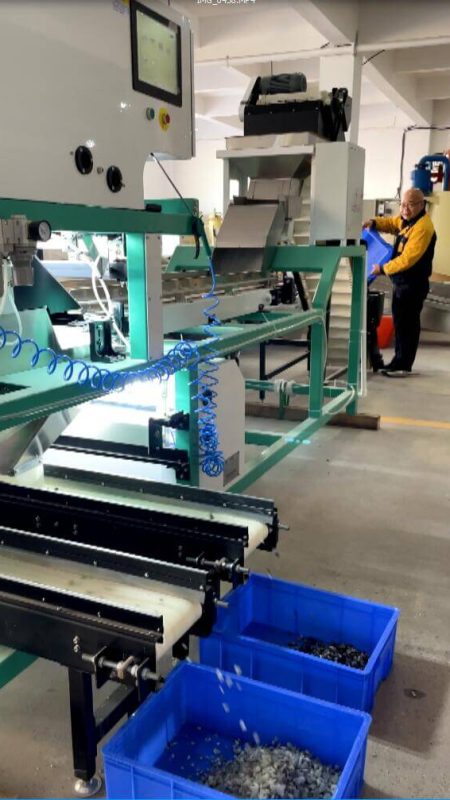
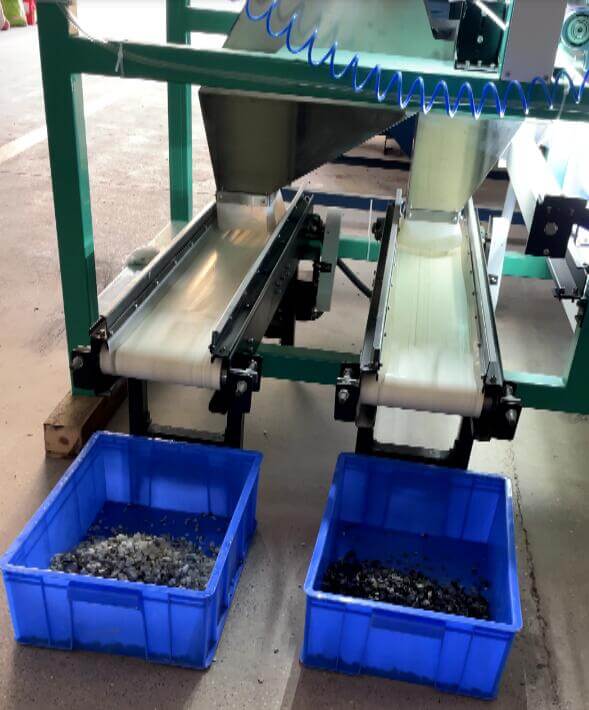
Step 5: Data Analysis & Performance Evaluation
The optical data collected during the testing phase is analyzed using advanced software and algorithms. We employ data processing techniques to extract valuable information from the optical signatures of the particles and evaluate the sorting performance based on predefined metrics and criteria. This assessment includes recovery rates, purity of the sorted fractions, concentrate grades, and waste rejection efficiency.
Step 6: Reporting and Recommendations
We prepare a comprehensive report summarizing the optical separation testing process, findings, and recommendations. The report includes an analysis of the sorting performance, economic considerations, potential benefits, and limitations specific to the mining operation. The recommendations cover optimization strategies, equipment selection, and potential integration of optical sorting into the existing processing circuit.
Equipment For Optical Separation
Commonly used equipment in lab mineral optical separation testing
- Feeding equipment
- Optical separator