Barite is an important industrial mineral used in various industries, including oil and gas drilling, paints and coatings, ceramics, and medical applications. However, barite must undergo beneficiation processing before being used in these areas. Given its wide range of applications, barite testing plays a vital role in determining the quality and characteristics of the mineral before large-scale processing and production. Among them, barite flotation testing is a key step in the mining and mineral processing. It accurately determines the efficiency and effectiveness of the flotation process, ensuring optimal recovery and quality of the final product.
Barite Flotation Testing Steps
1. Sample Preparation:
A representative sample of the ore is collected and crushed to a suitable size for further analysis. This ensures that test results accurately reflect the characteristics of the entire deposit. The collected ore sample is ground into a uniform powder, usually using a ball mill or other appropriate equipment to complete this step.
2. Crushing & Grinding
Once collected, these samples undergo a rigorous crushing and grinding process to achieve the particle size required for further analysis. The goal is to obtain a homogeneous material that is easily manipulated during subsequent testing phases.
- Send the collected samples to the laboratory or test site and crush the ore. A jaw crusher, hammer crusher or ball mill is usually used to break the ore into smaller particles.
- The crushed ore particles must be ground further to prepare for subsequent physical or chemical treatment. A grinding machine, such as a ball mill or rod mill, grind the ore particles finely. If necessary, the powder sample can be classified using sieves to remove particles that are too large or too small.
3. Physical testing:
(1). Initial testing involves visual inspection and color evaluation to determine if it matches the typical gray or light blue barite color. This step helps identify any impurities or changes in the appearance of the mineral.
(2) Another aspect of the process involves measuring the particle size distribution of the barite sample. It is usually done using techniques such as laser diffraction or sedimentation analysis, which provide valuable information about the average particle size and the distribution of different-sized particles within the sample. Yet another aspect is to assess the density of barite samples compared to water or other reference substances through specific gravity measurements. In barite testing, wet and dry densities must be measured to calculate an accurate specific gravity value.
(3) Other physical tests evaluating barite include screening analysis, bulk density measurements, porosity analysis, moisture content determination, and abrasion testing. Combined, these tests provide a comprehensive understanding of the various physical properties of the barite sample, which can provide insight into the mineral’s suitability for different beneficiation methods.
4. Test process design
Mineral processing tests are conducted in the laboratory using small-scale equipment to simulate production conditions. Such as gravity separation, flotation, magnetic separation, etc., to determine which method is most suitable for extracting the target metal from the ore. These tests may need to be performed multiple times to determine optimal beneficiation conditions. It also involves carefully considering factors such as ore characteristics, particle size, mineralogy and desired end-product specifications. Determine the properties and parameters of barite, such as concentration, reaction time, temperature, etc. These parameters will affect the metal recovery rate and mineral processing effect.
5. Flotation Testing
Flotation involves treating ground ore with water and suitable reagents to attach to barite particles selectively. This step will help separate the valuable minerals from the barite ore. Many factors can affect this selectivity, including the pH of the solution, temperature, concentration of the reagents used, and contact time between particles and reagents.
- In a flotation cell, a flotation agent, usually a specific chemical, is added to the slurry to help float the barite particles.
- Air bubbles are usually injected into the flotation tank to immerse the barite. As the bubbles rise, the barite particles are floated to the liquid surface to be separated.
- The flotation process produces tailings containing minerals that have yet to be extracted. These tailings often require treatment to reduce environmental impact and waste generation.
In barite flotation tests, various flotation scenarios were explored using different chemical combinations and operating parameters to maximize grade and recovery.
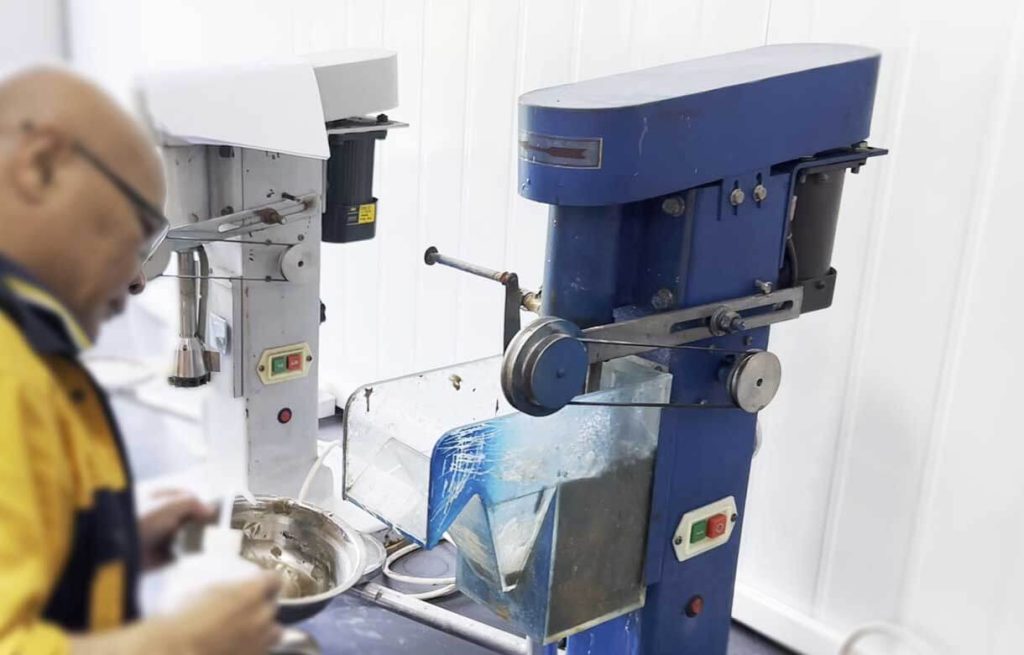
6. Analyze & Record results
The processed samples were analyzed to determine metal concentration and recovery. The mineral processing effect can be evaluated and optimized based on the experimental results. Record all experimental data, including sample information, chemical analysis results, testing parameters, etc. This data is important for subsequent decision-making and reporting.
Engineers and researchers can determine the best conditions to separate barite from other minerals and impurities through rigorous testing and analysis. The barite flotation testing process ensures the production of high-quality barite products and increases the efficiency and sustainability of barite mining operations. Producers can ensure maximum efficiency and quality while meeting industry specifications after determining beneficiation studies’ mineral composition and effectiveness through grinding, flotation, or magnetic separation. Asia-Africa International supports customizing mineral processing test services and equipment according to the specific conditions of minerals to strive for the maximum mineral recovery rate for you.