Hematite, also known as iron oxide, hematite is a widely recognized mineral with a distinctive reddish-brown color and metallic luster. Also, an abundant mineral found worldwide, it is the primary ore used in iron production. This iron oxide mineral is one of the world’s most important sources of iron, making it a key element for industrial development. Hematite beneficiation refers to removing impurities in ore by physical or chemical methods. However, hematite beneficiation testing ensures that hematite deposits are effectively processed to extract high-grade iron. This includes analyzing the ore’s chemical composition and physical properties to determine its ability to be processed into high-quality iron ore products. This testing also plays a key role in ensuring that final steel products meet industry expectations for strength, durability and performance. We will provide a complete lab hematite beneficiation test service to determine the optimum conditions for iron extraction from hematite ore.
Hematite Beneficiation Test Steps
Laboratory hematite beneficiation tests are important in evaluating hematite deposits’ mining and processing potential. These tests involve gravity separation, magnetic separation, flotation, etc., to separate the impurities from the ore.
1. Sample Preparation
Collect a representative hematite sample from the desired source first, ensuring that the sample is homogenized correctly. The samples should then be crushed and ground to a suitable size for laboratory testing.
2. Crushing & Grinding
Use a jaw crusher or similar equipment to reduce the size of the ore particles. The ore is then further ground to the particle size required for the test using a ball or rod mill.
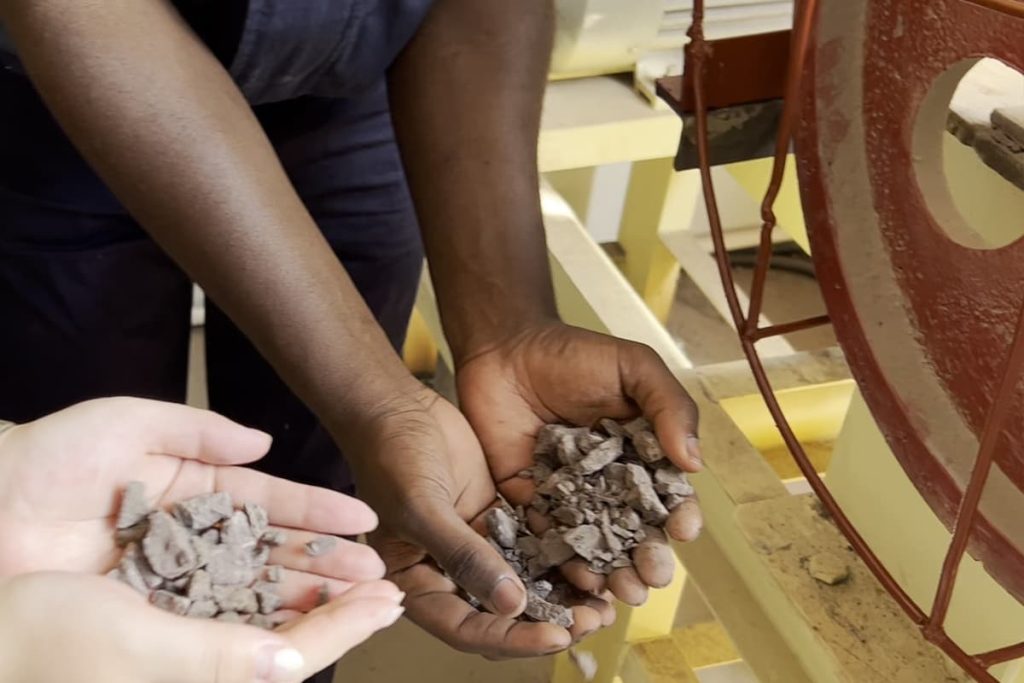
The comminution aims to obtain a suitable particle size for the subsequent beneficiation process.
3. Sample Analysis
The hematite samples were characterized in detail to determine their mineralogy and chemical composition. Analysis techniques involving X-ray diffraction (XRD), scanning electron microscopy (SEM) and chemical analysis can be used to understand the properties of ores. This analysis helps to understand the free characteristics of hematite and helps to choose the appropriate beneficiation method.
4. Magnetic Separation test
Evaluation of the magnetic properties of hematite and its suitability for magnetic separation techniques. Hematite is a strong magnetic mineral, and magnetic separation is a beneficiation process. Magnetic separation experiments were performed using a laboratory-scale magnetic separator to separate magnetic hematite from non-magnetic gangue minerals. Magnetic separators such as wet high-intensity or low-intensity magnetic separators can be used to determine magnetic separation performance. Adjust magnetic field strength and other operating parameters to optimize separation efficiency.
5. Gravity Separation Test
Gravity separation tests to assess the potential of gravity-based beneficiation methods. The difference in specific gravity between hematite and gangue minerals is used for separation—equipment including jigs, shakers or spiral chutes, etc.
6. Flotation test
Hematite beneficiation can also be achieved by froth flotation, taking advantage of the differences in surface properties between hematite and gangue minerals. Using various reagents, frothers and collectors, adjusting pH, reagent dosage and other flotation parameters to optimize flotation performance and obtain high-quality hematite concentrate.
7. Analysis and Optimization
The hematite concentrate or tailings obtained are analyzed to determine their chemical composition, iron content and impurity levels. This data will help assess the effectiveness of the beneficiation process and guide any necessary modifications. According to the test results of gravity separation, magnetic separation and flotation, optimize the processing parameters. This may involve adjusting grind size, reagent dosage or process conditions to achieve the desired concentrate grade and recovery.
8. Reporting
Compile the results from the hematite beneficiation tests and prepare a comprehensive report summarizing the findings. The information should include testing procedures, observations and recommendations for further steps in the beneficiation process.
Hematite Magnetic Separation Test
We provide a full range of lab mineral test services in order to choose the best process for you. Among others, this is our hematite magnetic separation test:
- Put about 100mm of hematite into the feed port of the jaw crusher, and crush the material to 20-30mm by squeezing each other through two tooth plates after starting.
- Put about 20-30mm hematite ore into the feed port of the hammer crusher. After starting, the hammer head and the material directly collide to crush, and then we will get a uniform 0-2mm placer.
- Pour the crushed material into the ball mill and add grinding steel balls. At this time, you can see that the ball mill will rotate continuously, and the grinding steel balls inside will grind the material into fine particles.
- Pour the 200-mesh material into the wet drum magnetic separator. The magnetic separator can reach 1200GS. There are two ore discharge ports, one for magnetic minerals and the other for non-magnetic minerals. Wet drum magnetic separator is suitable for roughing and beneficiating relatively coarse-grained strong magnetic materials, such as wet or dry magnetic separation of manganese ore, magnetite and other materials.
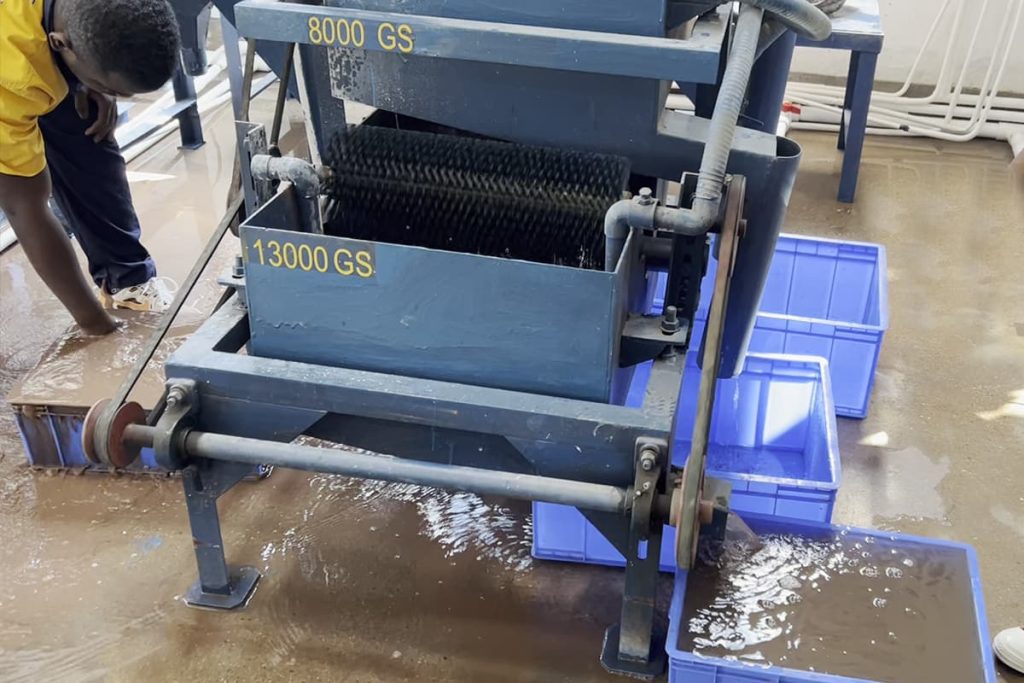
Asia-Africa International laboratory hematite beneficiation tests provide valuable insight into the process of separating hematite from other minerals. The test is a key step towards sustainable mining practices as it reduces waste and ensures efficient use of resources. Success has paved the way for further exploration and optimization of the beneficiation process to unlock more value from our mineral resources. Careful analysis and experimentation by our team have focused on developing a cost-effective process that can potentially increase the overall efficiency of iron ore processing plants. Our provision of advanced beneficiation testing services and equipment has been instrumental in achieving these positive results. We will continue to explore new solutions to optimize mineral processing operations to maximize the potential of our natural resources to meet the needs of various mineral processing plants.