Before we build a mineral processing plant, mineral testing are usually carried out to confirm the beneficiation solution and required equipment. The purpose of the raw ore test first is to check which equipment is most suitable for processing tantalum niobium ore, and the second is to examine the beneficiation effect of the processing equipment. By conducting mineral processing experiments and getting testing results, we can quickly confirm the most suitable processing plan for the tantalum niobium tin ore, avoiding detours. It is necessary to conduct beneficiation experiments before industrial beneficiation. In nature, tantalum and niobium associate with each other as oxides. Tantalum niobium ores refer to the general term for minerals containing tantalum and niobium. There are over hundreds of minerals in total. Among them, it is mainly tantalum iron ore, niobium iron ore, and pyrochlore are suitable for ore mining. Tantalum (Ta) and niobium (Nb) are rare metals with high melting points (Ta 2996 ℃, Nb 2468 ℃) and high boiling points (Ta 5427 ℃, Nb 5127 ℃). They have a steel-like appearance, a gray-white luster, and a dark gray powder. They have characteristics such as gas absorption, corrosion resistance, superconductivity, unipolar conductivity, and high strength at high temperatures, used for preparing oxide tantalum and oxide niobium and extracting tantalum, niobium, etc. We can get raw ore grade analysis information through a dedicated tantalum niobium ore acoustic analyzer.
Why do we need to conduct testing?
- Mineral processing experiments are a significant way to help you evaluate how to obtain the highest value during rock ore separation. If you have a mine but cannot select the ore, and the grade is high, it is also a “dull” ore.
- Mineral processing testing is the most excellent reference basis for formulating mineral processing plans and investment cost budgets, planning and implementing them to reduce development risks.
- Mineral processing testing is also the most effective manifestation of the value of mining rights transactions. They can verify the economic value of the development of the mine, reduce investment risks, and double the valuation of the mining rights.
- It’s the essential technical basis for beneficiation plants, as the properties of ores in different regions change from time to time, and even in the same mining area, the degree of ore oxidation is also constantly changing. Therefore, the conditions of mineral processing are also different. Before developing each type of ore, it is necessary to conduct beneficiation tests and choose the most reasonable and suitable mineral process way, rather than copying other’s similar beneficiation processes.
- The beneficiation test is also the basis for determining the rationalization of the beneficiation plant equipment, finding the optimal balance between investment, cost, indicators, and operational benefits, thereby reducing the initial investment and post-production costs and achieving maximum economic benefits for the mine.
- It can improve the condition of substandard products, low recovery rates, high costs, and comprehensive recovery of other minerals. By conducting testing, It will show new processing ways, flow charts, and equipment and develop to increase recovery rates and reduce economic losses.
What testing is for tantalum niobium ore?
1. Different crushed particle sizes will release different amounts of ore.
Laboratory equipment is required when the crushed ore is 0-2mm: Laboratory jaw crusher, laboratory hammer crusher, laboratory shaking table, and three disk-magnetic separators.
(1) First, we use a laboratory jaw crusher to crush the rock size under 20-30 millimeters and adjust the gap between the tooth plates to ensure that the particle size of the material is within 20-30mm.
(2) We use a lab hammer crusher for secondary crushing. It is necessary to break them down to below 2mm and release the tantalum niobium concentrate as much as possible from the stones. Only then can the subsequent beneficiation equipment achieve better results.
(3) The laboratory shaking table separates tantalum niobium tin concentrate and heavy minerals. The shaking table is a commonly used equipment for gravity separation, which separates heavy and light minerals with different specific gravity. Tantalum niobium-tin and other magnetic minerals are heavy minerals, and silicon dioxide is light minerals, preliminarily enriching the mixed concentrate of heavy minerals. The larger the difference in mineral-specific gravity, the better the beneficiation effect of the shaking table, and the more obvious the mineral separation. The recovery rate can generally reach around 75-85%. We first collect the concentrate from the shaking table, naturally dry it, and then enter the subsequent selection equipment.
(4) Since we have obtained the concentrate from the lab shaking table, which should be tantalum, niobium, tin, and other magnetic minerals, such as magnetite, ilmenite, and hematite. How do we separate tantalum, niobium, tin ore, and other magnetic minerals? We have to improve the grade of tantalum niobium and tin.
The recovery rate depends on the grade of these two minerals in the raw ore, as well as the grade of other minerals in the raw ore. Generally, tantalum and niobium grades can reach 40-60%. If we want a higher grade ore, we can carry out different solutions for tantalum-niobium ore processing, but the maximum ore recovery rate is around 65%.
2. Laboratory equipment is required when the crushed raw ore is 0-1mm.
Laboratory jaw crusher, laboratory hammer crusher, laboratory ball mill, laboratory shaking table, three disk-magnetic separator
Firstly, the 20-30mm raw ore from the jaw crusher will go into a lab hammer crusher for crushing to get an ore size of 0-2mm. We will screen the materials bigger than 2mm with a small circular vibrating screen and return them to the hammer crusher for crushing. Then put the 0-2mm material into a ball mill and grind it to 0-1mm. Finally, use a three-disc magnetic separator to screen out magnetic minerals.
3. When the crushed raw ore grinds to 200 mesh. Required lab jaw crusher, lab hammer crusher, laboratory ball mill+spiral classifier, laboratory shaking table, and three disk-magnetic separators.
The crushing section is the same as the 0-1mm discharge situation. The difference is that the ball mill will work with a spiral classifier or cyclone for classification. The coarse particles return to the ball mill for grinding, and 0-200 mesh fine particles enter the back-end beneficiation equipment. The default standard configuration is a ball mill+spiral classifier, which has a better classification effect and forms a natural closed circuit system with the ball mill.
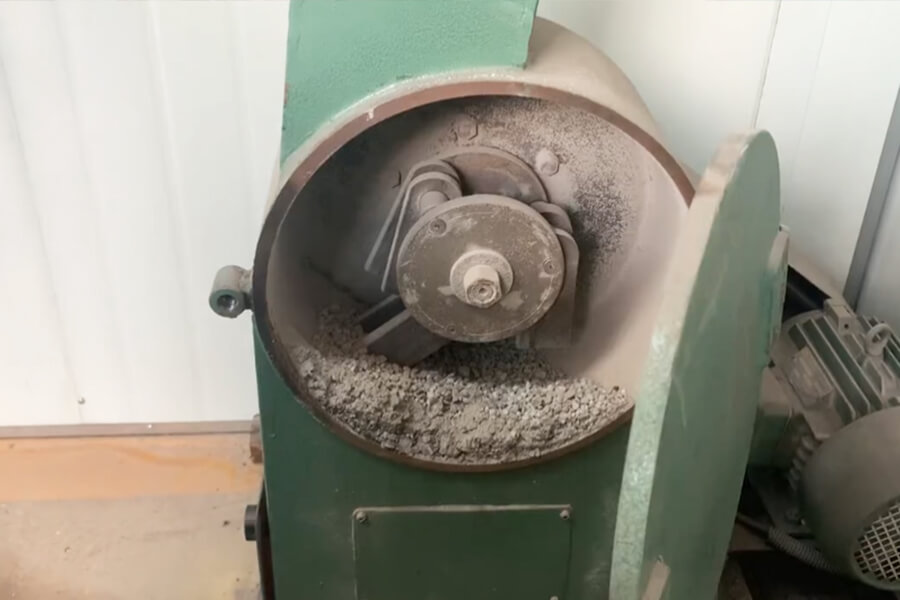
Asia-Africa International Mining and metallurgical research institute provide various mineral testing services, such as copper, iron ore, manganese, gold, lead zinc, quartz, china clay, etc. We provide accurate and reliable test results to meet the different needs of customers. Our advanced equipment, experienced engineers, and technical personnel help our clients better optimize their mining operations. Welcome to inquire and consult!