Chalcopyrite beneficiation is a strategic and important metal extraction mineral that requires various beneficiation processes to maximize copper recovery. The copper concentrate grade of copper pyrite is generally low, and it is difficult to improve the copper grade. In the laboratory, various methods can be used to evaluate the effectiveness of different processes and conditions to maximize copper recovery while minimizing gangue minerals. Chalcopyrite beneficiation test is the journey from raw ore to high-purity copper. It starts with crushing, releasing valuable minerals through crushing and grinding, and then processing using gravity separation and flotation processes. In laboratory chalcopyrite beneficiation, the main purpose is to evaluate the best beneficiation method to maximize the recovery of the concentrate.
What is Chalcopyrite
Chalcopyrite is a primary copper mineral composed primarily of copper iron sulfide (CuFeS₂). Due to its importance in copper production, chalcopyrite is often referred to as a mother ore. In addition to its economic value, chalcopyrite’s bright golden-yellow color and metallic sheen make it a sought-after item among collectors and enthusiasts.
In addition, chalcopyrite has a Mohs hardness of approximately 3.5 to 4, striking a balance between being soft enough to be easily manipulated and durable enough for practical applications. Its excellent electrical conductivity also makes chalcopyrite an interesting candidate for electronics research, potentially enhancing our understanding of sustainable materials for future technological advancements. Its unique structure enables innovative manufacturing of high-performance alloys and catalysts that could revolutionize multiple industries, including electronics and environmental remediation.
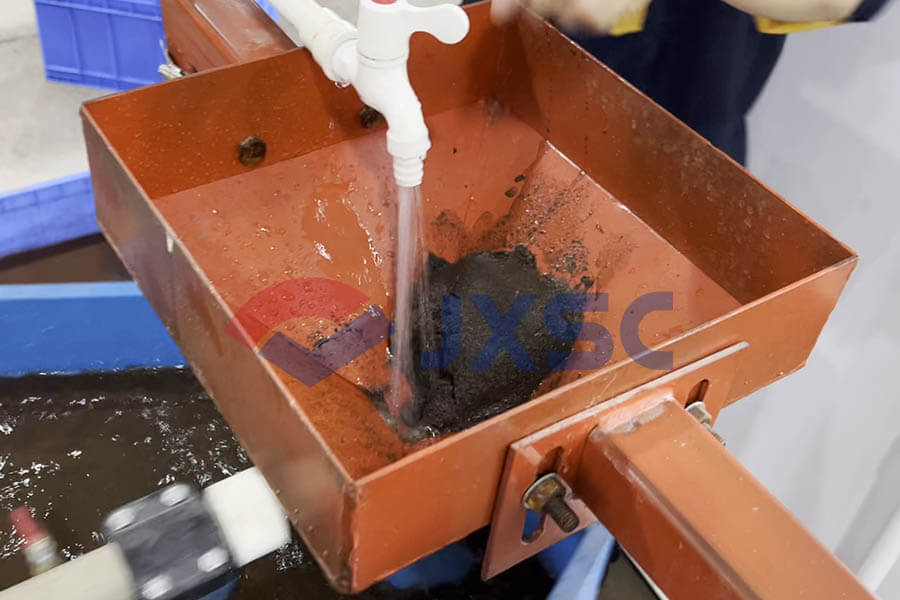
The purpose of chalcopyrite beneficiation testing
- Evaluate the efficiency of various flotation reagents because these chemicals have a significant impact on mineral separation. Understanding how different collector and frother combinations react with chalcopyrite can lead to innovative strategies that not only maximize yields but also minimize environmental impact by reducing agent usage .
- Determine the impact of grind size on concentrate quality and recyclability. By adjusting the particle size during the crushing process, researchers can find an optimal point where release is maximized without using too much energy. This focus on optimizing grind size not only improves operational efficiency but is also consistent with sustainability goals and promotes responsible resource extraction practices.
- Under the fluctuating system conditions of the flotation process, such as pH, temperature and ionic strength. Determining the stability of chalcopyrite in different environments allows mining operations to dynamically adjust their processes to ensure resistance to unforeseen changes during the production phase.
Chalcopyrite beneficiation test process
1. Sample Preparation:
Select representative ore samples, crush and screen them to ensure uniform particle size.
2. Mineral Analysis:
Usually, the process usually starts with crushing and grinding the ore to separate the chalcopyrite particles from the gangue minerals. The samples are chemically analyzed to determine their mineral composition and content and to evaluate the economic viability of the chalcopyrite.
Collect representative chalcopyrite samples. Grind the samples to a suitable particle size to improve the efficiency of the subsequent separation process to obtain a suitable particle size (usually 80% passing 200 mesh). Commonly used grinding equipment includes laboratory ball mills.
3. Flotation Test:
Flotation is a critical step that improves the recovery of chalcopyrite from gangue material. Factors such as pH and reagent selection can significantly affect separation efficiency, emphasizing the need for precise control.
Conduct flotation tests using flotation reagents (such as collectors, inhibitors, and foaming agents) and select appropriate reagent formulas and flotation conditions (such as temperature, pH value, etc.). Adjust bubble generation, skimming, and concentrate collection during the flotation process. Carry out flotation experiments of roughing, concentrating, and sweeping and record the recovery rate and grade.
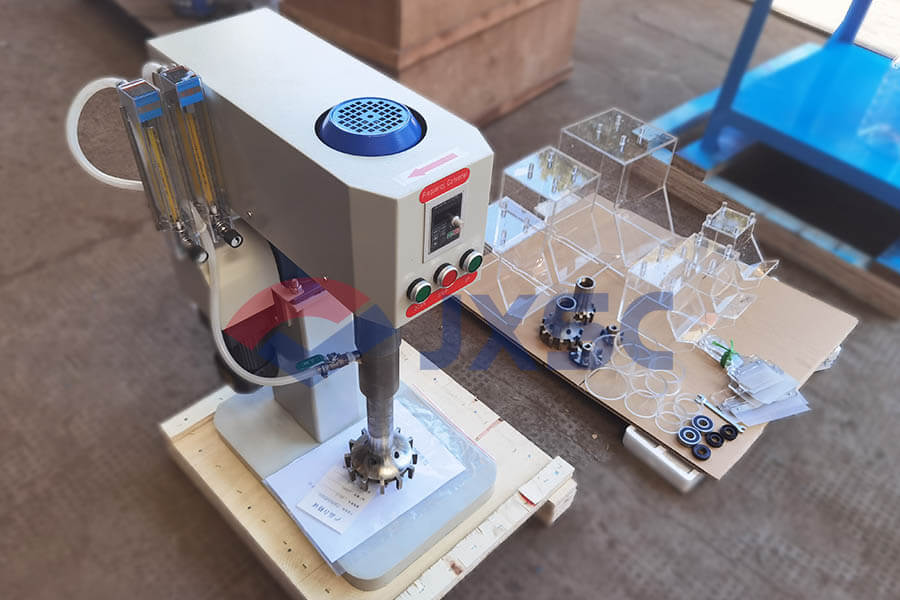
4. Gravity Separation Test
Often overshadowed by conventional flotation technology, it is a compelling alternative due to its lower operating costs and environmental impact. This technology is often used to pre-concentrate ore before further processing by taking advantage of the inherent density difference between chalcopyrite and gangue minerals. A spiral separator or shaking table is usually used in gravity separation test.
The pre-processed chalcopyrite concentrate is placed in a gemini shaker table. Using mechanical shaking and water flow are used to separate the ore particles by density. The minerals are clearly zoned on the bed and the concentrate can be clearly seen.
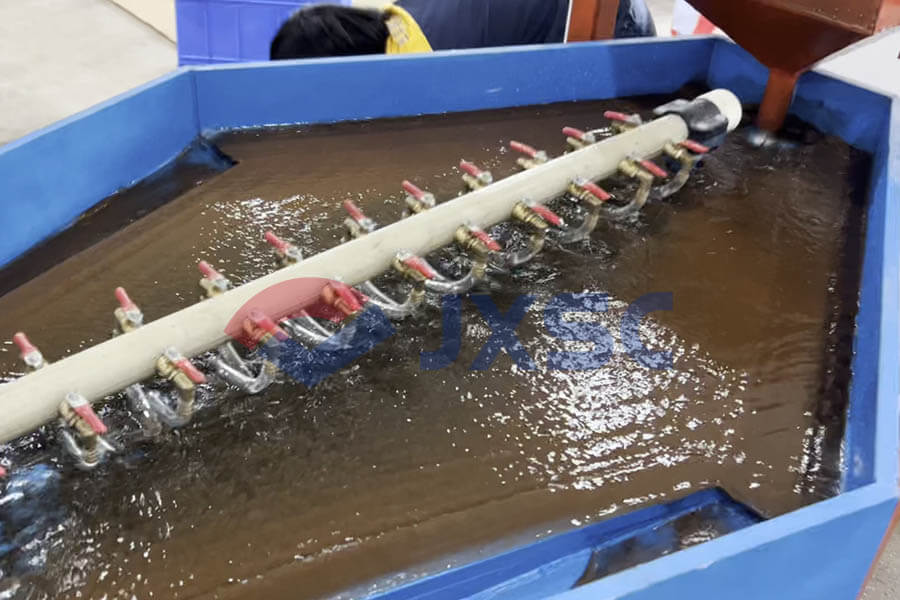
5. Sedimentation test
Carry out sedimentation test on tailings after flotation to evaluate the treatment and utilization of tailings. Screen and grade concentrate and tailings to ensure that products of appropriate particle size are obtained.
6. Finished product evaluation
Carry out composition analysis and recovery rate calculation on concentrate to evaluate the effect of mineral processing technology. Summarize test data and analyze mineral processing effects under different conditions. Write experimental report and put forward suggestions for improvement and industrial application.
Process interpretation of laboratory chalcopyrite beneficiation tests can provide key insights into optimizing extraction methods and improving overall recovery. By systematically analyzing variables such as particle size, reagent selection, and flotation conditions, researchers can develop customized strategies to improve the efficiency of chalcopyrite processing. Asia-Africa International provides professional mineral processing testing services and laboratory mineral processing equipment, contact us for more details!