Solid/Liquid Separation
Effective solid-liquid separation is essential to the plant’s overall performance and represents a substantial capital investment and operating and maintenance cost. Asia-Africa International supplies laboratory solid-liquid separation testing services to help you with optimal dewatering and metals/product recovery in mineral processing. Our tailored Solid/Liquid Separation technologies and processes facilitate optimum mineral reclamation and solids/product dewatering to low moistures with low cycle times.
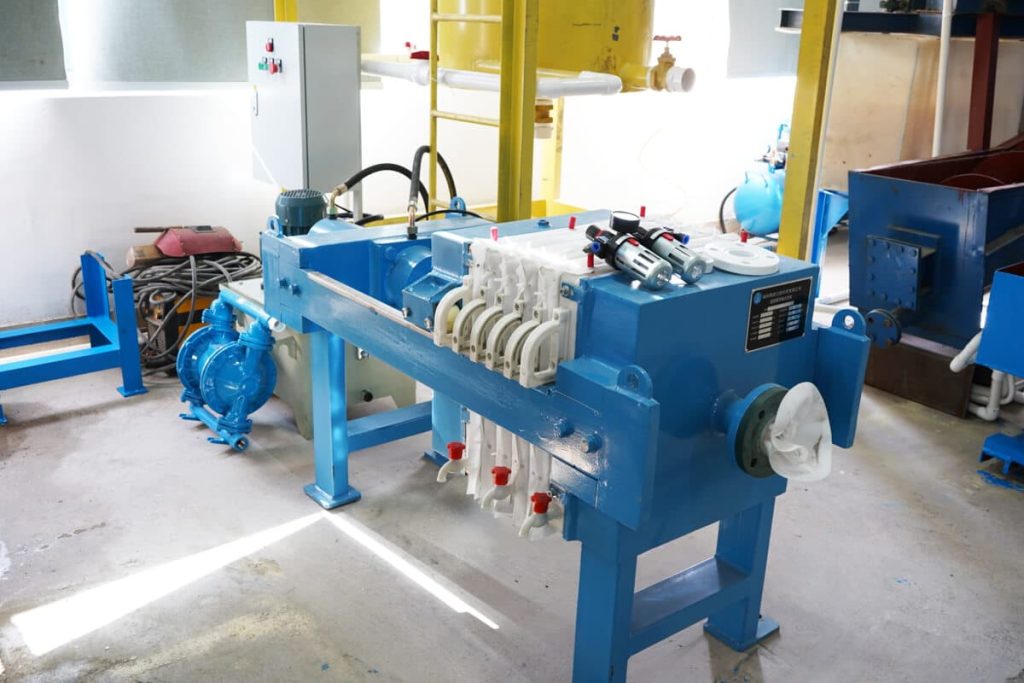
Lab Solid/Liquid Separation Testing
Introduction
Solid-liquid separation is an essential link in mineral processing, separating solids from liquids.
The solid-liquid separation in the beneficiation process mainly refers to the dehydration of concentrate and tailings. The dehydration process is divided into three stages:
- Concentration and dehydration process
- Concentration-filtration-dehydration process
- Concentration-filtration-drying dehydration process
There are many essential methods of solid-liquid separation. The concentrator will choose different solid-liquid separation methods according to different process links. The commonly used dehydration methods are gravity dehydration(natural gravity dehydration, gravity concentrated dehydration), mechanical dehydration( sieving dehydration, centrifugal force dehydration, filtration dehydration), drying and dehydration, magnetic dehydration, physicochemical dehydration, and electrochemical dehydration.
Work Principle
1. Gravity Dehydration
- Natural gravity dehydration: It is a method of dehydration by using the gravity of the surface moisture of the material particles, such as the dehydration work of the dehydration bucket of the coal preparation plant and the coal dehydration of the dehydration bin.
- Gravity concentration and dehydration: rely on the gravity of the fine-grained material to settle in the liquid to achieve solid-liquid separation, such as the concentration and dehydration of concentrators and sedimentation tanks.
2. Mechanical Dehydration
- Screening and dehydration: Dehydration relies on the inertial force generated when the material and the screen surface are in relative motion, such as the dehydration work of a linear vibrating screen.
- Centrifugal force dehydration: separating solid and liquid by centrifugal force, such as dehydration of filter centrifugal dehydrator and sedimentation centrifugal dehydrator.
- Filtration dehydration: a solid-liquid separation process in which the liquid passes through the filter medium to retain the solid, and the separation is accelerated by negative or positive pressure, such as dehydration of vacuum filter, plate, frame filter press, pressure filter, etc.
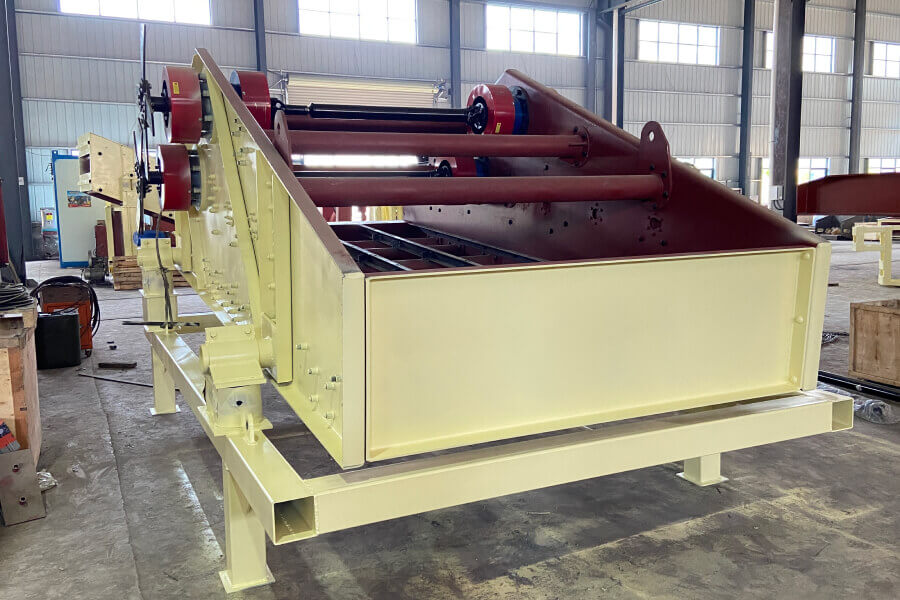
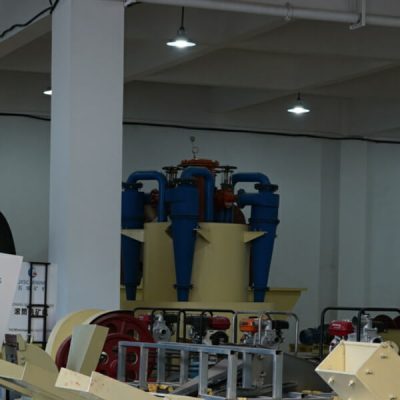
3. Drying and Dehydration
A dehydration method uses heat energy to vaporize and evaporate the water in the material, such as thermal drying and sunlight exposure.
4. Magnetic Dehydration
A solid-liquid separation method is achieved by using the magnetic force generated by a magnetic field on magnetic minerals, such as a magnetic dehydration tank.
5. Physical and Chemical Dehydration
Instead of other ways, it uses water-absorbing objects or chemicals (such as quicklime) to absorb water to achieve solid-liquid separation.
6. Electrochemical Dehydration
Under an external electric field on the solid mixture, water molecules move to the cathode with positive charges, and fine solid particles move to the anode with negative charges, thereby realizing solid-liquid separation.
It is necessary to separate the liquid and solid phases at different stages or the end of processing in the mining industry. This operation performs thickening and filtration. Asia-Africa International can perform laboratory studies on the settling parameters of a slurry and the selection of the most appropriate flocculating agents. Concerning filtration, Asia-Africa International has laboratory filters with which it can also study essential parameters such as filtration time, filtering capacity, etc.
As a famous dewatering solutions manufacturer and global Solid/Liquid Separation specialist, Asia-Africa International’s extensive range of industrial filter presses, centrifuges, and water treatment processes increase the separation rate and overall process efficiency, energy efficiency & minimize waste, environmental compliance, reduce capital and operating costs and prolong equipment life and improve safety. So choosing us to do the mineral solid/liquid separation testing is an intelligent choice.
Main Testing Steps
Step 1: Sample Preparation
Obtain a representative sample of the mixture or suspension that needs to be separated. This may involve collecting a sample from a process stream or preparing a synthetic mixture in the laboratory.
Step 2: Testing Selection & Operation
Select the appropriate solid-liquid separation operation mode according to the material and demand.
Centrifugal sedimentation
The centrifugal sedimentation method separates the solid particles in the mixture from the liquid by rotating at high speed. This method is suitable for solid particles with smaller particles and higher density.
Filtration
The filtration method intercepts the solid particles in the mixture through a filter medium with a small pore size to realize solid-liquid separation. This method is suitable for solid particles with larger particles and lower density.
Screening
The screening method is to sieve the solid particles in the mixture through a sieve to achieve solid-liquid separation. This method is suitable for solid particles with larger particles and lower density.
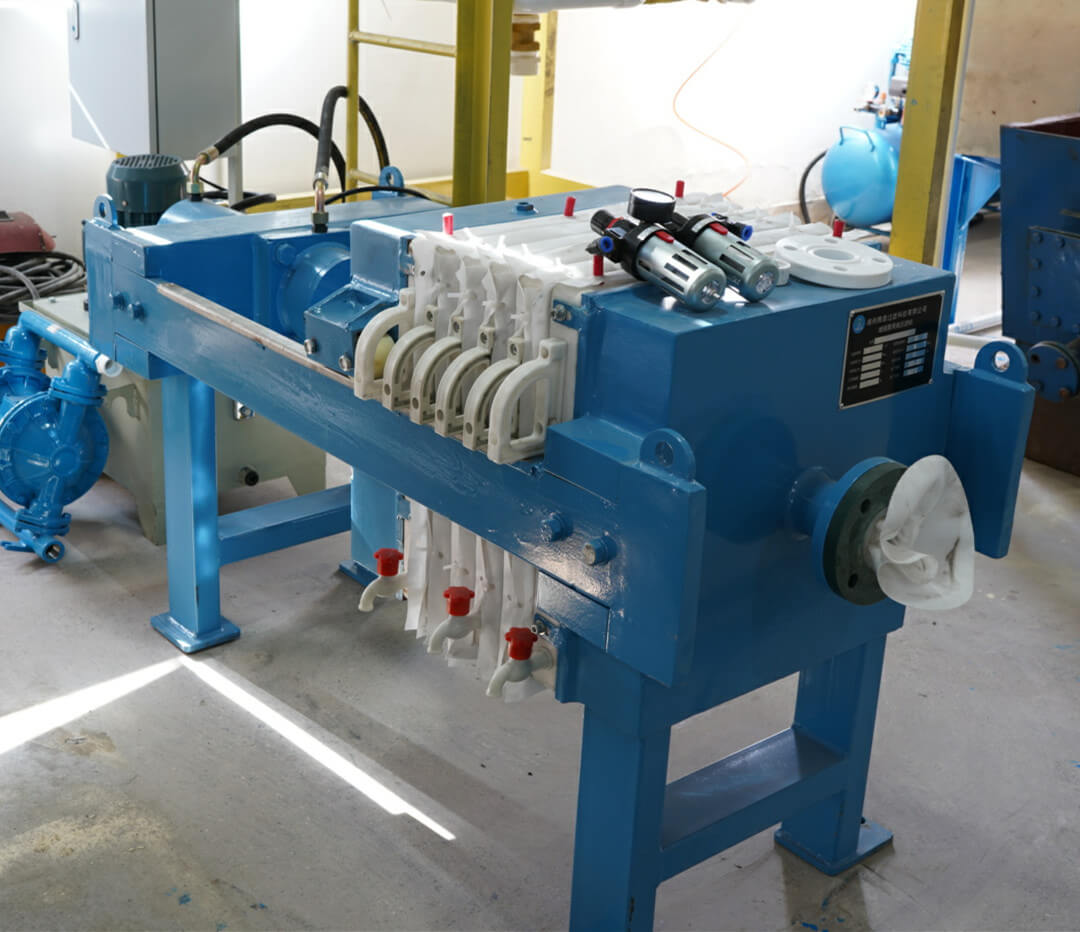
Step 3: Analysis and Reporting
The separated solid and liquid fractions may be further analyzed to determine their composition, concentration, or desired properties. The test results are recorded, analyzed, and reported, providing information for process optimization or equipment selection.
Equipment For Solid/Liquid Separation Experiment
Commonly used equipment in lab mineral solid/liquid separation testing
- Settling tanks
- Thickeners
- Sedimenting centrifuges
- Hydrocyclones
- Dewatering screen
- Vacuum Disk Filter